Corrosion is an irreversible natural process that causes a slow and continuous wear of metal, resulting in a deterioration of the material’s characteristics or physical properties. It is essential to protect all metal surfaces so that this does not diminish the functionality of products and structures, as well as generating serious economic damage and safety risks.
Corrosion is a process of slow and continuous deterioration of a metallic material caused by the oxidation of its surfaces. There are many causes of oxidation and resulting corrosion, but the most common one is the attack of atmospheric agents or liquids, known as corrosives, which come into contact with the metal surface.
In the ISO 8044 standard, the International Organisation for Standardisation has in fact defined corrosion as the physicochemical interaction between a metal and its environment that results in changes in the properties of the metal and that may lead to significant impairment of the function of the metal, the environment, or the technical system.
Basically, corrosion is the tendency of metal bodies to transform themselves over time by losing their original properties, deteriorate, and return spontaneously to the state in which they are found in nature, i.e. that of combination with other elements, in particular with oxygen, from which they had been removed in the metallurgical processes by the administration of energy (electrical, chemical, or heat). This is why corrosion is also called anti-metallurgy.
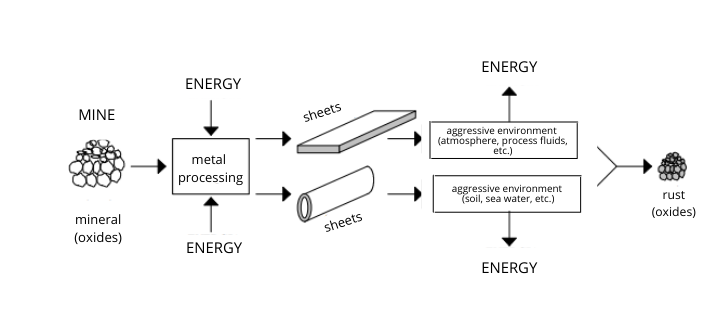
Although the phenomenon of corrosion can affect different materials, as the above-mentioned standard points out, it is often associated with metallic substrates, i.e. metals and their alloys, even those that are naturally provided with a passivating layer. In particular, corrosion affects carbon steel, stainless steel, and aluminium alloys processed into sheets, extrusions, and profiles.
How does corrosion develop?
Two elements are therefore needed to give rise to corrosion:
- electrochemical processes involving the metal (electrode);
- the corrosion environment (electrolyte).
Most metals occur in a stable form in nature. In order to achieve stability with less energy, a metal atom loses one or more electrons from its structure; these combine with other elements in the environment, such as oxygen, sulphur, or chlorine, and they cause the metal to oxidise.
Environments and corrosion mechanisms
Depending on the environment in which it takes place, corrosion can be classified as follows:
Dry corrosion does not occur in the presence of water or humidity, but when the metal is exposed to certain substances, such as sulphur dioxide, hydrogen sulphide, sulphuric acid, etc., which give rise to oxidation.
The substance that most commonly binds to metal causing its oxidation is oxygen.
Dry corrosion always occurs at high temperatures.
Corrosion in a wet environment occurs in the presence of water, oxygen, and elements of a chemical nature (acid rain, detergents, insect secretions, etc.) or of a physical nature (temperature, mechanical stress, etc.).
The factors that most influence corrosion vary in different climatic conditions and in different rural, industrial, or marine areas. The action of aggressive chemicals in the atmosphere in combination with high humidity can lead to rapid degradation of metal due to the thin liquid film formed, which acts as an electrolyte and, depending on its characteristics, can strongly affect the extent of corrosion. This film tends to form when the environment reaches a critical humidity threshold.
In order to classify the corrosion behaviour of materials operating in different locations, four environment categories are normally used:
- rural environment: locations away from sewers and coastal areas.
- urban environment: residential or commercial locations with low pollution levels.
- industrial environment: locations with the presence of heavy industries (chemical/metallurgical).
- marine environment: locations near a coast.
Other forms of corrosion
Physical-mechanical corrosion is caused by electrochemical and mechanical stresses induced on the part from the outside or the inside, thus generating fretting corrosion, fatigue corrosion, or stress corrosion.
There also exist corrosion phenomena of a biological nature resulting from contact of the metallic material with biologically active water or soil.
Morphology of corrosion phenomena
Metal surfaces can be affected by as follows:
Generalised corrosion
As the name suggests, this type of corrosion affects the entire surface of a metal object and it results in its thinning. We distinguish between as follows:
- uniform corrosion, when it affects an entire surface and the severity of its effects is consistent at any point;
- non-uniform corrosion, when it affects an entire surface, but its effects are more or less evident at different points.
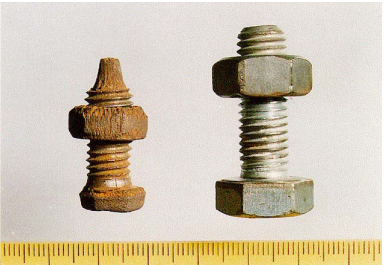
Localised corrosion, or pitting
The term “localised corrosion” is used when the phenomenon affects only specific points on a surface. This takes the form of localised attacks, also known as pits or pitting, ranging in size from a few tens of microns to a few millimetres. The affected area may present different morphologies, including ulcers, craters, pinpricks, grain edges, etc.
This form of corrosion is considered more dangerous than generalised corrosion, because it is less visible to the naked eye.
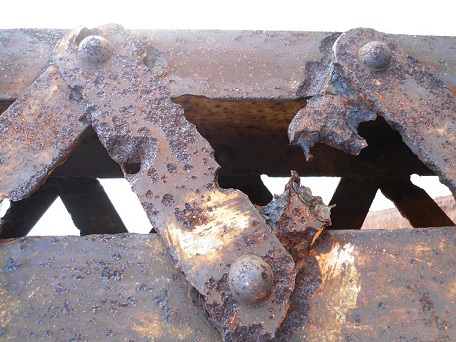
Selective corrosion
“Selective corrosion” indicates the phenomenon that causes the preferential dissolution of a constituent of the metallic material that is more easily attacked for chemical or metallographic reasons. It mainly affects metal alloys and it involves the preferential dissolution of the less noble metal by exposure to medium corrosion environments; the nobler metal, which is not attacked, remains in the metallic state in the form of a porous residue. The most common examples include the so-called dezincification of brass and grating of cast iron.
Protecting metals from corrosion
Metals are used to manufacture buildings, infrastructure, cars, and many other objects around us. In all these cases, although a natural phenomenon, metal deterioration due to corrosion is actually not welcome. This is why it is important to protect metal surfaces properly. First of all, it is worth remembering that some metals, including those nobler than steel, such as silver, copper, lead, nickel, and chrome, either do not need to be protected as they do not corrode or they are coated to improve their aesthetics. On the contrary, steel needs to be protected by active or passive systems.
Passive protection avoids contact with metal by applying a thin impermeable layer that isolates its surface from aggressive agents and/or by adding suitable chemical compounds, including organic coatings (paint) and metal coatings (zinc, nickel, chrome). Active, or cathodic, protection on the other hand, prevents the formation of corrosion by transforming all anodic points on the metal surface into cathodic points with the supply of an electric current.
An economic problem
So far, we have dealt with corrosion from a technical point of view. However, we must not forget that this phenomenon also entails economic issues. Each year, the damage caused by corrosion to the environment, people, and property is estimated to run into millions of Euros. It is also estimated that about one fifth of annual steel production is intended for replacing parts damaged by corrosion.
A sign on a stand at the 2002 NACE-CORROSION trade fair, the industry’s main event held in a different US city each year, read: “While you read this sign, 30,000 kg of iron are corroding,” which emphasises the wide spread of corrosion.
In addition to reducing the functionality of materials, corrosion needs to be combated because it can have negative consequences both in environmental terms – e.g. gas and oil pipelines and platforms that could cause ecological disasters – and in terms of safety – e.g. fastening systems or structural parts of bridges, trains, and aircraft, whose failure due to corrosion could have dramatic outcomes.
Morandi Bridge (Genoa, Italy). © Il Sole 24 OreProperly protecting metals from corrosion is therefore essential. Although this may entail a high upfront expense, proper and effective corrosion protection actually helps save money and resources in the long run.
Case in point: the Eiffel Tower
France’s most famous monument, built by Gustave Eiffel for the 1889 Exposition Universelle to commemorate the centenary of the French Revolution, is made of iron with a low carbon content.
Every 7 years, the Eiffel Tower is completely repainted to protect the metal from rust and corrosion caused by air pollution and bird droppings. Each time, this operation takes about 14 months, 25 workers, 50 tonnes of paint, and very high costs, which could have actually been lower. According to a study by a German expert, if the Eiffel Tower had been hot-dip galvanised, its maintenance interval would have been 17 years, thus saving more than $10 million.
Moreover, during the last restoration operation that began in May 2019, the workers realised that the 19 layers deposited previously had deep cracks in several places, so that it was impossible for a new layer of paint to adhere. Therefore, they have had to scrape off the previous layers on 10% of the structure, removing approximately 30 tonnes of paint, and then apply 60 tonnes of new coatings. The cost of this operation, which will end this year, is more than 40 million Euro.