Corrosion is present in our everyday lives more than we think. The progressive deterioration it causes can have devastating effects and weaken essential structures such as the metal reinforcements of bridges. In this article, we will try to understand if and how corrosion may have influenced the partial collapse of a bridge that first became a symbol of engineering innovation and then of an unforgettable tragedy: the Polcevera Viaduct, known to everyone as the Morandi Bridge.
The most famous bridges for their strength and durability have always been the Roman ones: built in wood, stone, or concrete, many of them are still standing and still widely used.
The Romans had particularly developed the masonry technique of using concrete. However, since ancient times, the deterioration phenomena observed in structures made of this material have pushed people to prefer other construction solutions. Let us see why.
Concrete, which is still widely used in construction nonetheless, has a strong compressive strength but it is weaker in terms of tensile strength. Therefore, architectural structures made in this material are reinforced with metal elements (the most common nowadays is steel) which are “embedded” in the concrete mass and called “reinforcements” or “reinforcing bars (rebars)”. Hence the name of “reinforced concrete” or “reinforced cement concrete”.
Reinforced concrete has good tensile strength and provides wall material with a long service life. However, it is heavy, it has poor thermal and acoustic insulation, it is sensitive to moisture, and it is prone to degradation.
Furthermore, especially in past centuries and before the industrial revolution at the end of the 19th century sanctioned its success with large-scale production, one of the reasons why other materials were preferred to it was the chemical reaction called “carbonation”, caused by the contact of cement with carbon dioxide and creating cracks into which moisture and water can penetrate. These, in turn, affect the elastic properties of metal reinforcements, already burdened by the mechanical fatigue to which they are subjected. The metal does not only lose its resistance and resilience, but it also expands; in some cases, the stresses resulting from such expansion break the concrete, thus considerably weakening the structure and leading to the possible collapse of portions or entire sections of bridges.
In is also true that from the very beginning, irrespective of the construction material chosen, bridges have always been subject to collapses, in which the sudden lack of self-supporting capacity due to various reasons has resulted in a high number of casualties and inestimable direct and collateral damage.
Why do bridges collapse?
When the news about a bridge collapse spreads, the common feeling is that the event occurred suddenly and without any actual triggers. With the exception of collapses that are the consequence of natural phenomena such as earthquakes, floods, landslides, fires, or road or rail accidents, understanding the reason for the collapse of a bridge structure is essential to prevent these exceptional events from happening again.
The most common causes are as follows:
- design defects
- unsuitable construction material
- lack of inspection and maintenance
- corrosion of metal reinforcements.
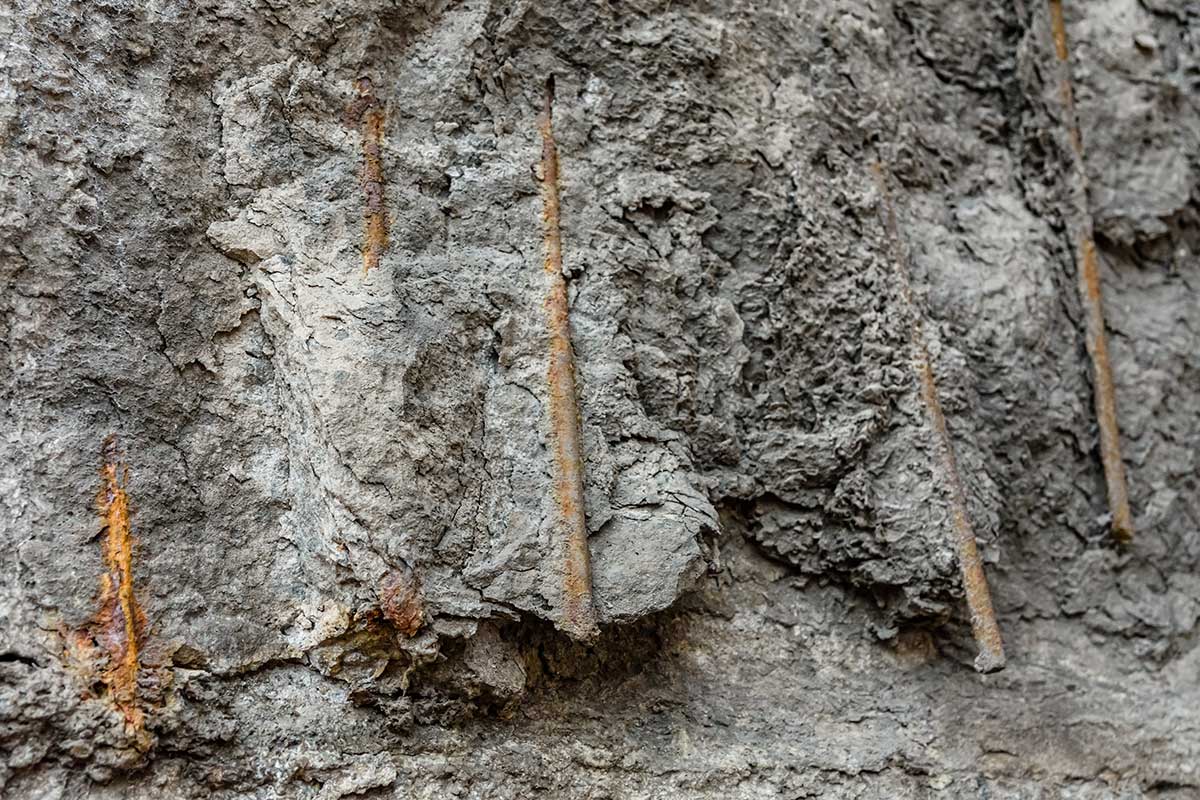
Over the past twenty years, about 130 bridges have collapsed worldwide for a variety of reasons. How many cases were directly caused by the corrosion of metal reinforcements?
Corrosion of metal reinforcements in reinforced concrete
As can be read in the blog article exploring its most important aspects, corrosion is a natural and irreversible process that causes slow and continuous wear of the metal in which it is triggered. If its action is not detected and therefore interrupted in time, this phenomenon leads to the inexorable decomposition of metal.
In the case of concrete’s reinforcements, the chemical attack triggering corrosion occurs when the metallic elements bind with oxygen, water, or other acids present in the environment, thus forming layers of ferric oxide and other substances that attack the metallic elements themselves to the point of weakening them over time. The process of iron oxidation thus occurs, resulting in the formation of the red-brown patina known as “rust”. Because of oxidation, iron expands, increasing its volume considerably and causing the expulsion of a 3-4 cm thick concrete called “concrete cover” precisely because its function is to protect the metal reinforcements. Subsequently, this patina tends to flake off. This considerably diminishes the thickness of the rebars, which lose both their volume and their strength. This starts a slow process of degradation that leads to the weakening of the entire structure and, if action is not taken quickly and effectively, to its collapse.
In order to compensate for the lack of tensile strength in reinforced concrete, the use of so-called “pre-stressed reinforced concrete” became widespread towards the end of the 19th century. Nowadays, this is obtained by immersing a pre-stressed and tensioned metal reinforcement made of steel strands, a set of six cables wrapped around a central one, in the concrete mass. However, like the bridges’ support reinforcements, such strands, usually placed inside the tie rods that make up the anchoring system of pre-stressed concrete bridges, are also subject to the attack of corrosion. This can be avoided by coating the pre-stressed steel with suitable protective materials or by pouring concrete in-situ.
One of the first designers to make extensive use of this construction technique was engineer Riccardo Morandi, whose cable-stayed viaducts precisely feature tie rods made of pre-stressed reinforced concrete.
The collapse of the Morandi Bridge
The partial collapse of the Morandi Bridge in Genoa on 14 August 2018, which caused the death of 43 people, is still very much in the memory of Italians and many others.
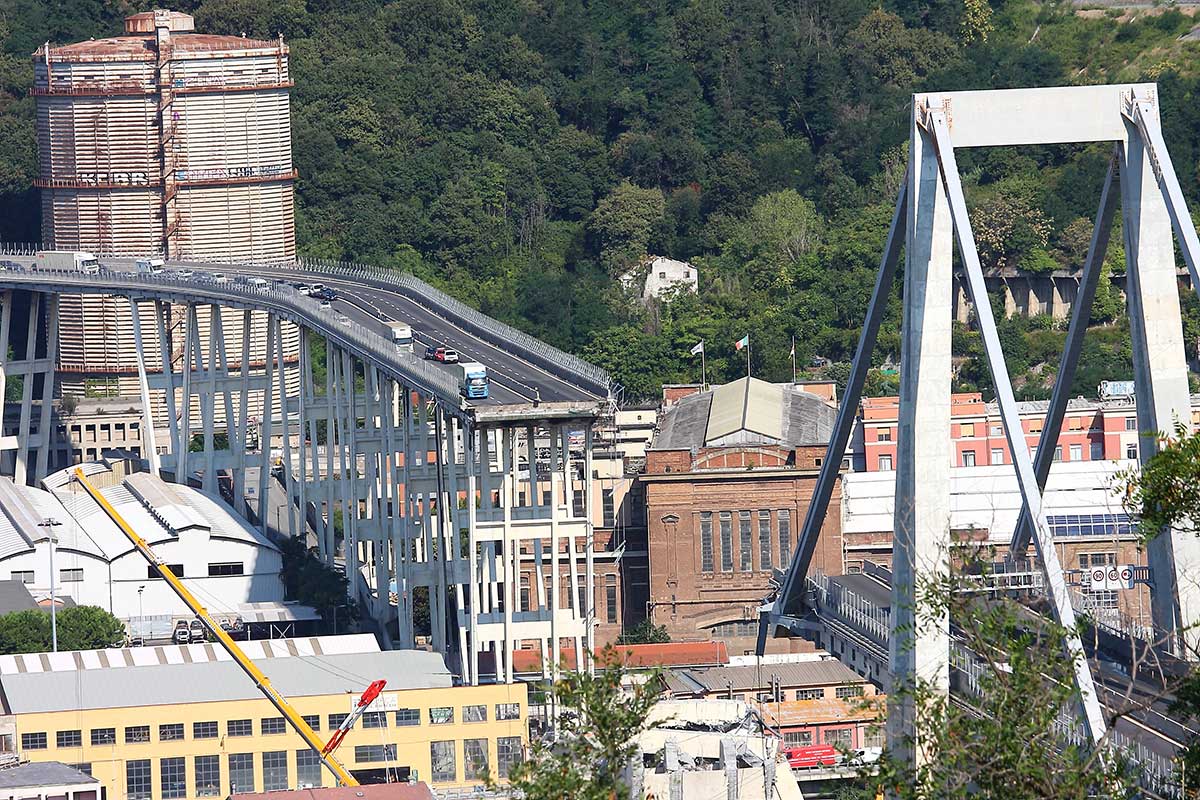
The cause is currently the subject of a judicial investigation, in which one of the first expert reports identified corrosion of the steel strands of the tie rods of pylon 9 of the bridge, the one that collapsed on 14 August, as one of the possible reasons. In fact, the experts found “a generalised, long-term corrosive state [in the cables], due to the presence of water moisture and the simultaneous presence of aggressive elements such as sulphides and chlorides [...]. 68% of the strands in the primary group, located inside the tie rod, and 85% of those located further out, showed a cross-section reduction of between 50% and 100%.” However, the defence of ASPI-Autostrade per l'Italia, one of the companies sued as possibly responsible or jointly responsible for the collapse, stated that “the corrosion percentages shown in the expert report’s table confirm that the load-bearing capacity of the stays was amply guaranteed, as was also demonstrated by the analyses carried out by the Empa laboratory in Zurich and the University of Pisa. Therefore, the possible presence of a very small percentage of strands corroded by up to 100% can in no way have affected the overall strength of the bridge.”
It is not our task to go into the merits of the judicial process. What we would like to analyse here is the influence that corrosion can have on the collapse of a monumental structure such as a motorway viaduct.
The designer’s awareness
The Polcevera Viaduct, inaugurated in July 1967 and now replaced by the new Saint George Bridge, was 1,102 m long and consisted of 11 bays created by 12 pylons. Pylons 9, 10, and 11 overlooked the Polcevera valley and were designed by Morandi as balanced systems, in which the deck was supported by pre-stressed concrete tie rods, called stays, which connected the deck itself to the top of the trestle masts, up to 50 metres high from the bottom of the valley.
© Roberto BrumatBased on the report
written by Morandi himself in 1979, i.e. twelve years after the inauguration of the Polcevera Viaduct, and made public a few days after the collapse, the designer was aware of the weaknesses of his work. He commented the slow deterioration of concrete as follows: “As is well known, apart from possible problems due to specific static deficiencies, a reinforced concrete bridge is subject to slow deterioration due to:
- the effect of moving loads and of environmental action, especially on flooring, load-bearing structures, joints, and finishes;
- the chemical and mechanical effects of weathering on concrete and rebars.
A separate category includes some special phenomena such as the presence of diffuse cracks (wall cracks), due partly to the poor expansion of concrete compared to steel (when the latter is subjected to high stresses), partly to vibrations caused by traffic, and partly to an uneven distribution of reinforcements within the concrete mass.”
The weak points of the Polcevera Viaduct
The Morandi Bridge was exposed to a high-salinity environment due to its proximity to the sea and to polluting emissions from industrial activities located in the area below. As a strategic motorway link between Northern Italy and Southern France, it was crossed by an average of around 30 million vehicles a year[1]. Traffic volume – and the stresses it could generate on the bridge’s structure – was considered an element to be monitored already in the 1979 report, which also noted a significant increase in vehicle traffic compared to that predicted in the design phase. Morandi stated that such increase had caused the formation of some isolated rust stains in places where, due to construction errors, the concrete cover’s thickness was lower than that calculated in the design phase. In fact, he wrote, “it seems that the structure is lashed by sea winds (the sea is about 1 km away), which blow into the valley crossed by the viaduct. Therefore, this stands in a highly saline atmosphere, with the wind also encountering a curtain of smoke from the steelworks’ chimneys on its route toward the viaduct and, therefore, being saturated with highly harmful vapours.”
© Riccardo MorandiThe first maintenance work
“In the wall structure, apart from a few minor faults in the execution, which caused some rust stains to appear in isolated areas due to the insufficient end coverage of reinforcements, the project provided for the insertion of steel elements inside the concrete, except, of course, for the cadmium-coated plates of the deck abutments. All these plates were literally corroded in just over 5 years by the extreme aggressiveness of the atmosphere and they had to be replaced with stainless steel elements in a rather complicated operation. We must think about what the maintenance costs would have been if a steel-only structure had been chosen instead of a reinforced concrete one, or at least if a solution had not been adopted with cables embedded in concrete shells under compression and, therefore, not subject to cracking. In addition, in recent years, the external surfaces of the structures and, in particular, of those exposed to the sea and attacked more directly by acid fumes from the industrial chimneys are beginning to show the signs of an aggression of chemical origin. This is obviously due to the formation of soluble salts resulting from the combination of the acids in the fumes with the free lime in the concrete (carbonation, ed.): the well-known loss of chemical resistance of the concrete itself. I believe that sooner or later, probably within a few years, it will be necessary to resort to a treatment consisting of removing all traces of rust on the exposed parts of the metal rebars, coating the damaged parts with epoxy resins, and covering the entire structure with elastomers featuring high chemical resistance.”
Internal strain
Since then, the history of the Morandi Bridge has been dotted with complex and frequent maintenance operations. From the outset, the difficulties associated with the impossibility of visually inspecting the steel cables inside the concrete-coated tie rods were stressed by several parties. However, in spite of this difficulty, the designer himself reiterated the need for a total retrofitting work, even in the years following his first reports on the viaduct’s state of deterioration. In 1981, he wrote about the tied rods, warning of the “need for a close, “hands-on” check of the steel by X-ray inspection.”
During one of the most extensive maintenance operations on one of the tie rods on the north side of pylon 11, carried out in 1992 with the addition of external cables, a construction defect was detected that could affect the tightness of the tie rods themselves. This is what the person in charge of the project, engineer Gabriele Camomilla, said in an interview with the Ingenio magazine a few days after the bridge collapse. “The bridge was the subject of very careful and constant inspections, even at the top of the pylons 90 metres above the ground. During one of these checks, we discovered that, on the last portion of a stay, at the top of the structure of pylon 11, [...] the concrete had left a portion of steel uncovered and this had led to corrosion by dissolution of approximately 30% of the strands. It should be emphasised that the stresses to which the stay-bearing steel was subjected (about 7,000 kg) were far less than the resistance capacities of its constituent material (15,000 kg).
“The construction defect was as follows: the very high-strength cables should have been spaced so that they would all be encased in concrete, which provides steel structures with considerable corrosion protection; due to a construction defect, however, all of the stays were packed at the top, so they were not well encased in concrete. This allowed part of the air to pass through and thus steel to be attacked.”
On that occasion, no major reinforcement work was planned for the stays of pylons 9 and 10, but only consolidation operations.
Corrosion as a trigger for collapse
What is striking about the first expert report investigating the origins of the viaduct’s collapse is the lack of inspection documentation on the stays after the 1992-93 analyses and interventions.
“No tests similar to those carried out in the three-year period 1990-92, in particular direct investigations into the state of pre-stressing cables, were carried out, or at least there is no trace of them.”
After the 1993 works on pylon 9, a “continuous reflectometric control system to check the state of deterioration” was installed, consisting of a sensor that, as engineer Camomilla recalls, was supposed to assess the external deformation of the cables. It worked with a modem connected to a computer and it measured the voltage intensity of the cables themselves.” The sensor actually operated from 1992 to 1996 and, once detection stopped, it was never replaced.
The inspection tools available in the 1990s are certainly not comparable to those of today. Nonetheless, the need to install a monitoring system, however simple, indicates that there were doubts about the stays’ resistance already at the time.
In their report on the collapse, the experts confirmed that “the cause of the collapse of the Morandi Bridge is the corrosion to which the upper part of the southern tie rod on the Genoa side of pylon 9 was subjected. Such corrosion process began in the early years of the bridge’s life and continued unabated until the structure collapsed, leading to an unacceptable reduction in the area of the resistant section of the strands that formed the core of the tie rods, essential elements for the stability of the bridge.”
© La RepubblicaWe can therefore conclude that corrosion undoubtedly contributed to weakening the strands of the tie rods of pylon 9, thus wearing down the structure from the inside, and led to its collapse on 14 August 2018, 51 years after its construction. It was only thanks to the special system designed by Morandi, with isolated modules independent of the neighbouring pylons, that the collapse only affected the part of the bridge connected to pylon 9, allowing the evacuation of motorists suspended on the nearby slabs and avoiding an even greater tragedy, which would have affected the densely populated area and the industrial and railway area below.
How can corrosion of metal reinforcements be avoided?
In order to prevent the corrosion of metal reinforcements, it is possible to repair the deteriorated concrete with different types of maintenance strategies. However, the preliminary inspection and control of the structure under analysis is always essential.
How can one tell if rebars are corroded?
One of the difficulties immediately identified by those responsible for the maintenance of the Morandi Bridge was the impossibility of naked-eye estimating the conditions of the strands embedded in concrete. However, the cracks detected a few years after the bridge was built had already been considered a warning sign by the builder himself.
Today, there are different methods for checking the corrosion status of metal inserts in-situ. These include visual inspections and structural monitoring systems with automatic, continuous acquisition capability, which, in the case of reinforced concrete bridges, detect cracks, deformations, and abnormal movements of the structure through sensors or radars connected to specific software. Other methods are magnetic tests using a pacometer and electrochemical tests such as potential mapping.
Let us look at the latter in more detail:
- Pacometer tests are carried out using a digital instrument capable of measuring the presence, direction, and diameter of rebars inside reinforced concrete elements in a non-destructive
way. It also allows measuring the thickness of concrete covers and rebar spacing. This inspection system belongs to the group of the so-called magnetic methods, as it uses the magnetic properties of iron to locate rebars.
- Potential mapping, on the other hand, is an electrochemical method that involves determining the reference potential value with a device placed on the concrete surface, using a damp sponge to guarantee electrolytic contact. This makes it possible to define the extent and intensity of the corrosive phenomenon on the reinforcement bars caused by a decrease in the alkalinity of concrete, due to carbonation phenomena or attacks by aggressive substances.
In the case of pre-stressed steel tie rods, however, the measurement of the potential is made difficult by the presence of polymeric or metallic strand cover sleeves. In addition, unlike conventional steels, pre-stressing steels can show other forms of corrosion such as stress corrosion, hydrogen embrittlement, fatigue corrosion, and fretting corrosion.
This is why, in 2004, a monitoring system called MuRE (Multi Reference Electrode) was developed, consisting in positioning a series of electrodes along a strand that can detect the onset of corrosion wherever it occurs.
In any case, the monitoring of the status of a bridge is only effective if it is accompanied by timely maintenance.
What can be done if rebars are corroded?
Several methods can be used to prevent corrosion of metal reinforcements in concrete. It is possible to increase the protective capacity of concrete by adjusting the water/cement ratio or by using mix cements whose formulation contain elements such as fly ash, blast furnace slag, or natural pozzolan, which significantly limit the penetration of chlorides into concrete products.
However, if a structure is located in an environment that is very conducive to corrosion, as in the case of the Polcevera Viaduct, more radical prevention measures should be taken, including as follows:
- the replacement of traditional metal reinforcement with stainless steel, a material more resistant to attack by chlorides;
- the coating of reinforcements with thermosetting products called “epoxy resins”, which create an effective protective layer as they solidify;
- the galvanisation of metal, whereby a zinc coating is applied to the metal substrate;
- the use of corrosion inhibitors, i.e. chemicals that, when added in small concentrations, can slow down the corrosion reaction by up to more than 95%;
- the use of the cathodic protection method, an electrochemical technique based on the coupling of two metals with different natural potentials: the steel of which the reinforcing bars are made and the zinc of the anodes; because concrete acts as the electrolyte, connecting the two metals generates a direct current that protects steel against corrosion;
- the coating of reinforcements with special mortars for restoring deteriorated concrete called “thixotropic mortars”, which is one of the most widespread methods, as well as one of the cheapest.
In the case of corrosion of the strands in pre-stressed concrete structures, repair work is aimed at consolidating the cables and restoring pre-stressing conditions. Here, it is possible to intervene with passive restoration systems through the application of unidirectional fabric in materials reinforced with polymer matrix fibres, carbon bars, B450C steel bars, or beton plaqué or with active restoration systems through external pre-stressing.
[1] This figure refers to a 2009 study by Autostrade per l’Italia on the Genoa Bypass, which found that the Polcevera Viaduct was crossed 25.5 million times a year, with an expected increase of around 30% over the next 30 years.